Pressure sensors enhance manufacturing with data support
With the general trend of industrial automation and intelligent manufacturing, the efficiency and product quality of industrial production have been greatly improved, developing in a more flexible, efficient and sustainable way. In this industrial process, we cannot ignore the important role of a component- pressure sensors. In this article, we will discuss the role of pressure sensors in various processes in industrial production, the installation and maintenance during application.
- Precise measurement and control: Pressure sensors can accurately measure pressure changes in industrial processes, which is critical for process control and product quality. For example, in environments such as oil refining and chemical plants, proper pressure maintenance is key to preventing accidents and ensuring personnel safety.
- Predictive maintenance: Pressure sensors can be integrated into predictive maintenance systems to predict potential equipment failures through real-time data monitoring, reduce unexpected downtime, and improve equipment reliability and service life.
- Process Control and Optimization: Pressure sensors can monitor and regulate airflow, hydraulic pressure, and gas pressure in industrial machinery to optimize production processes. With real-time data feedback, equipment parameters can be adjusted to increase efficiency and output.
- Intelligent monitoring and data analysis: Piezoresistive pressure sensors integrated into intelligent manufacturing systems can collect and transmit large amounts of data, which can be used to analyze and predict production trends, thereby improving production efficiency and product quality. Real-time analysis of sensor data helps to detect problems in a timely manner and take preventive measures.
- Increasing safety: In industrial automation, pressure sensors are used to monitor and control pressure conditions that can have an impact on safety, such as in hydraulic and pneumatic systems, thus increasing safety in the workplace.
- Heavy-duty equipment performance maintenance: Heavy Duty Pressure Sensors are used to monitor pressure, fluidity, flow and level of critical systems such as pneumatics, light-duty hydraulics, brake pressure, oil pressure, transmissions, etc., to maintain the performance of heavy-duty equipment.
Pressure sensors are used in various parts of industrial manufacturing to ensure precise control of processes, improve productivity and product quality, and enhance operational safety. In practice, it is not to be ignored to standardize the use of pressure sensors to ensure the safe and efficient conduct of industry.
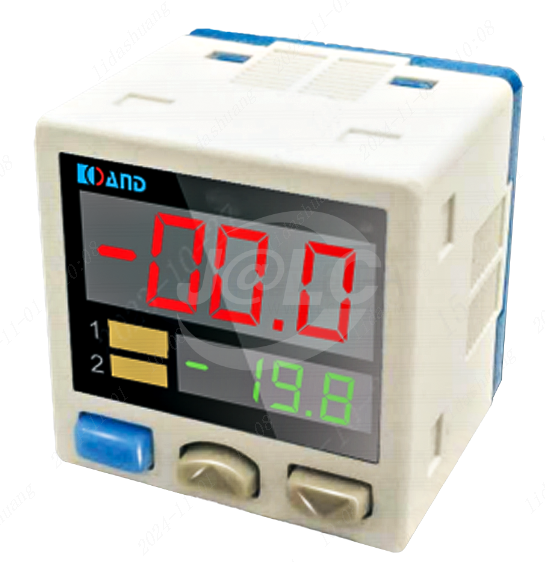
The following lists the basic steps from installation to maintenance of pressure sensors, which can provide a further understanding of their use.
Proper Installation of Pressure Sensors:
- Choose the right pressure sensors type based on the gas, liquid or steam you want to measure.
- Consider the temperature and humidity in the measurement environment to ensure that the pressure sensors can function properly.
- Select a location that is easy to maintain, clean, and less susceptible to mechanical vibration and shock.
Pressure sensors installation steps:
- Prepare tools and materials, including pressure sensors, mounting bracket, pipe, sealing gasket, screws, etc.
- Clean the pressure interface to ensure that there are no impurities and oil.
- Install the sealing gasket to ensure that the gasket fits tightly against the interface.
- Place the sensor gently on the sealing gasket to ensure that the sensor is aligned with the interface.
- Fix the sensor to the mounting bracket with screws to ensure that the sensor does not loosen or tilt.
- Connect the pipe to the outlet of the sensor to ensure that the connection is tight and leak-free.
- After installation, test and calibrate to ensure the accuracy and reliability of the sensor.
Maintenance:
- Check the connector of the pressure sensors regularly and remove it for cleaning to maintain accuracy.
- Avoid overloading, ensure that the sensor operates within the range, and prevent pressure "shocks" or sudden changes.
- Ensure that the measured medium is free of impurities and particles to avoid clogging the sensor.
- Before making any repairs or replacing components, the system power must be turned off and the medium in the pipeline must be emptied.
- Pay attention to comply with all applicable work safety standards and regulations, including explosion-proof requirements and wire protection measures.
Conclusion
The diverse role of pressure sensors in the performance of industrial machinery not only improves production efficiency and product quality, but also enhances safety and reliability. And its installation and maintenance of pressure sensors are key steps to ensure their long-term stable operation and accurate measurement. With the continuous advancement of technology, the application areas of these sensors will become more extensive, contributing to the development of the field of industrial automation.
JLCMC now offers piezoresistive pressure sensors that are capable of directly converting measured pressure into an electrical signal output with high accuracy and sensitivity; the small size allows them to be integrated into a wide variety of equipment and systems. New members who register now can enjoy $19 coupons. Click the picture to participate.
